AssetWorks have over 40 years experience in fleet management, therefore we understand the best practices when it comes to optimising fleets. Here we review some of the best ways to keep your fleet running smoothly and efficiently while taking advantage of the newest technology.
1. Keep your data clean
This may be the least compelling of the best practices on this sheet, but it also may be the most important. Most fleets today rely on multiple software systems to track everything from their vehicles and staff, to processes such as payroll and procurement. With so much dependency on your data, it’s important to make sure that your data goes into the system clean and stays clean as it’s used. Wherever possible, use automated data imports from trusted sources (such as your ERP system) instead of manual entry. This will improve accuracy and save time. When you must enter data manually into any system, simple things such as establishing picklists instead of text fields can greatly help with data consistency and integrity.
2. Understand the difference between imported data and integrated data
Importing is a step above manual entry. However, it’s useful to grasp the difference between imported
data and integrated data. Data imports are often one-way, which means that data is pushed from one system into another. Integrated data is often two-way and involves data verification in both systems. For example, many fuel systems can require drivers to input an odometer reading at the time of fueling and most fleet management systems are capable of importing that data from a flat file. However, the drawback to this method is that drivers can simply key in 9,999 or make up a meter reading in order to proceed with fueling. Integrated data would stop that from happening. In an integrated system, the meter reading at the pump is verified in the fleet management system before it’s accepted to start fueling. If a driver enters a fictitious reading or a reading that is well outside normal parameters, then the system won’t let them fuel.
3. Make your most important data visual
Determine what each person in your organization needs to know in order to best manage their work day. A technician may need to know how many open work orders exist against his scheduled time. A fleet manager may need to see how many vehicles are available to perform certain tasks. Once you determine the data points, illustrate the information in an easy-to-understand dashboard. Users are notified if and when any pre-set dashboard parameters are not met. Alerts can be sent to let an employee know that something is out of sorts and needs to be investigated or handled. By placing dashboards in a location that people see frequently, such as an electronic bulletin board or the home page of their computer, it’s easy to direct people to the most pressing issues.
4. Set up standard/scheduled jobs
Whether you purchase standard labour times from a service such as Motor Information Systems or calculate the average time to do certain jobs from your own maintenance history, creating standard jobs is critical to improving the efficiency of your fleet operation. Keeping track of the standard labour time, bill of materials, and resources needed to complete certain work order types can make it easier to plan technician and facility time.
Standard jobs also provide a greater benefit when you use them to automate processes. For example, you can set up workflows that automatically close work orders that fall within those standards or require technicians to input notes on work orders that fall outside those standards. Standard/scheduled jobs also facilitate the planning of work, allow for more accurate out-of-service estimates and help accurately set customer expectations regarding unit availability.
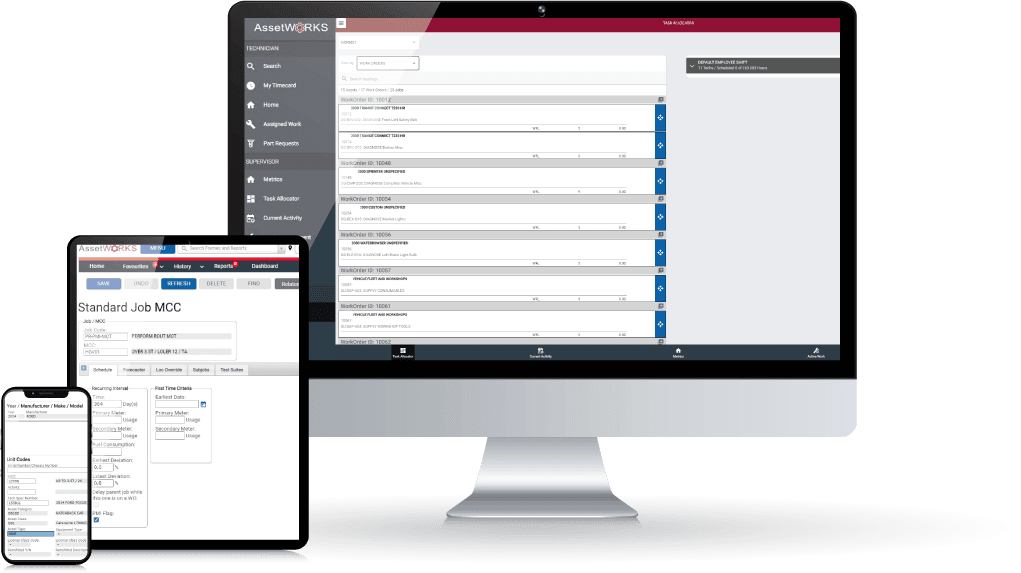
5. Report on the exception, not the norm
With the amount of information you have to manage, exception reporting is essential to help focus your attention on the right area. To accurately report on exceptions, you must invest time to identify what is ‘normal’. This involves industry research or analysis of historical data to establish certain anticipated or preferred parameters for data points, such as vehicle MPG or percentage of available units. Exception reports highlight the data that falls outside of the expected parameters. This can help draw your attention to the situations that need to be addressed so that corrective action can be taken
6. Proactively schedule your shop’s work
Planning is a basic tenant of business success, yet many fleet organisations don’t plan at the work order level, which can leave them reacting to changing fleet conditions instead of taking control. By monitoring PM schedules, tracking standard jobs and managing resource availability, fleet managers can optimize their workload. This can lead to improved vehicle availability, and reduced fluctuations in the labour budget which come from technicians’ non-productive time or overtime.
7. Be transparent
Today’s world demands a high level of transparency. The instant access to information that has become commonplace in today’s consumer environment is setting a high level of expectation for both your internal customers and management team. Providing clear, transparent information makes good business sense. Being transparent creates confidence in your organisation and shows just how well you are running your fleet. Some fleets opt to publish monthly or annual reports on their websites. Others opt to create customer-facing dashboards that provide up-to-date information on relevant information, such as fleet availability or services needed.
8. Let your vehicle talk to you
A vehicle’s on-board computer captures an immense amount of information and there are many tools to transmit that information directly into your fleet management system. From diagnostic computers in the shop to advanced GPS solutions, there is a way to gather this information on nearly every budget. It’s what meaning you apply to this data that defines the real value. By creating automated communication between your fleet management system and your fleet vehicles, you can automate processes based on data that comes directly from the vehicle’s onboard computer. This is useful to gather information, such as meter readings and oil temperature, as well as actionable items, including diagnostic trouble codes (DTCs) and driver behaviour, such as idle time. DTCs can be configured to create service/work requests and notifications to the fleet manager.
9. Don’t leave money on the table
If you aren’t adequately tracking warranties for your vehicles, components and parts, you could be losing money through unnecessary part and repair purchases. It begins by making sure your warranties are tracked with your vehicle and part records in your fleet management system so that if a work order is opened, you can easily assess if the repair or part should be covered under warranty. Tracking warranty claims in your fleet management system creates a digital paper trail and can help you manage the whole process, from identifying the warranty work through to claim retrieval and reconciliation.
Many people don’t chase warranty pennies, because it requires time and they may not have the staff levels to handle it. In this case, we recommend clients use past warranty repair information in the purchasing cycle. If you configure the OEM warranty parameters in your fleet management system to identify all repairs covered by warranty, you can use this information during the replacement planning process. Understanding the amount of warranty repair work done can help you understand whether you spend more on certain manufacturers and the data can also become a bargaining chip when negotiating prices.
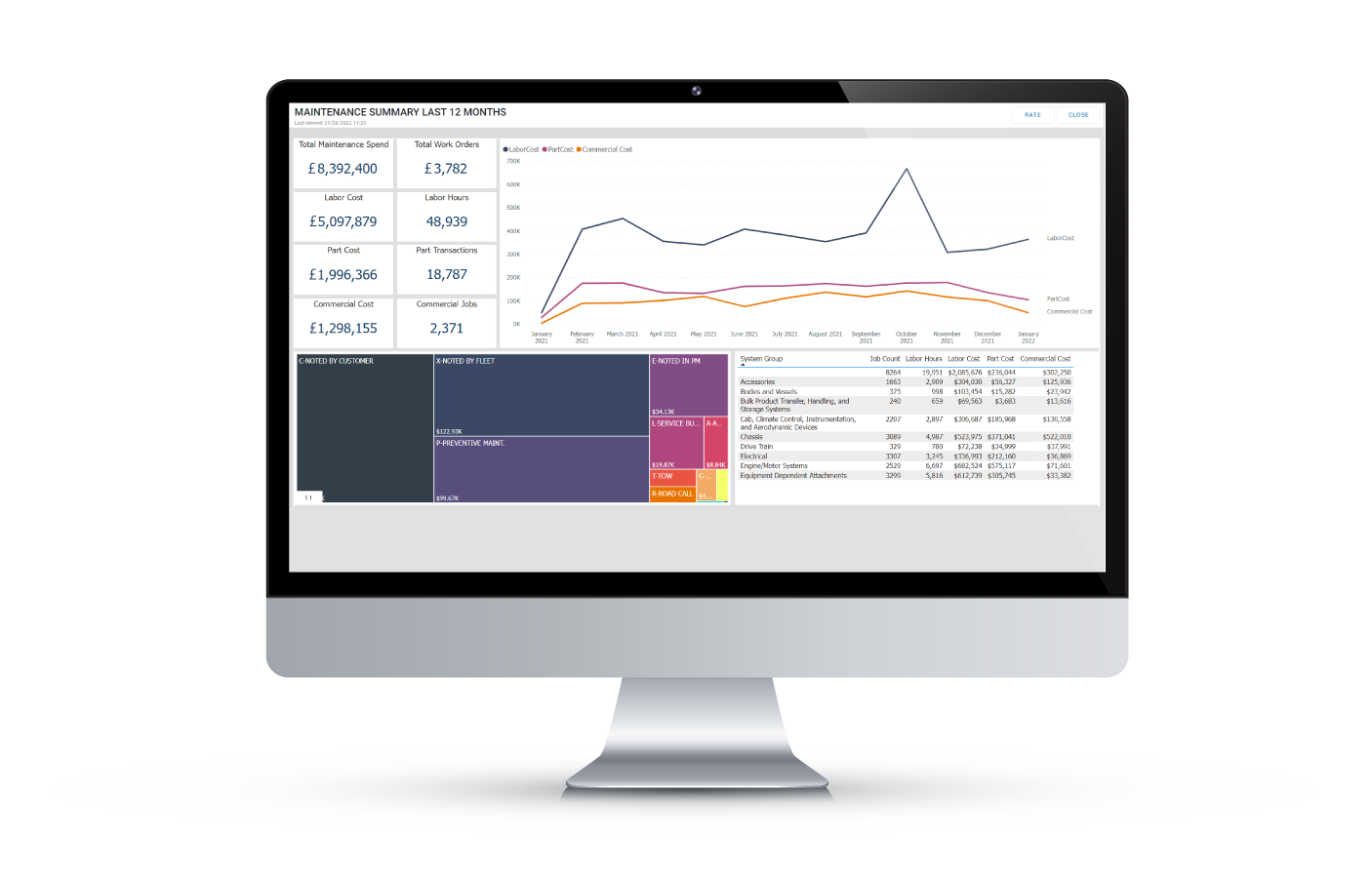
Looking to improve your fleet management operations?
In this ecosystem there is FleetFocus, a core product for fleet management. FleetFocus allows customers to create preventative maintenance schedules, track inventory, optimise data reports and much more. AssetWorks has a wealth of seamless integrations to equip fleets with successful software for transitioning to EV, elevating your telematics usage, or expanding the control of other assets.